Reactors
Think of what you have
learned about reactor engineering so far. The first step of analysis is to find the proper set of
elementary reactions described by balanced chemical equations. Each equation proceeds at a
rate given by the rate equation (the rate coefficient as well as the activation energy can usually
be found in tables). Reaction stoichiometry can be included in the description of the problem by
means of the reaction progress z, and the rate equation can be transformed into a differential
equation for [z]. This equation must be solved, giving the time course of [z](t) and at the same
time the time courses of the concentrations of all the species involved in the reaction. This
solution corresponds to the ideal batch reactor,
which is a vessel filled at time zero by reactants,
which are mixed so intensively that the concentration of species is homogeneous, i.e., the same
at any point in the reactor. Then the concentrations depend only on the process time measured
from batch start-up. But, as you have probably noticed, most apparatuses (furnaces, reactors)
where the reactions take place, are continuous and operate in the steady state mode, i.e., all
concentrations are independent of time! Does this mean that the previous results are
inapplicable? Or, what is an equivalent of time in this case? Such a time scale is the time
interval between the instants when the reactants enter and leave the apparatus, the so called
residence time. If the residence time is the same for any particle (molecule) entering the system,
it is reasonable to assume that all particles move like a solid, like a plug or piston - for a model
of plug or piston flow,
see Fig. 8.13:
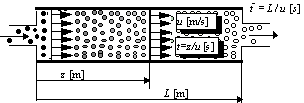
In this case the results from a batch process also hold for the continuous system, using the
residence time t=z/u as a process time (or mean residence time L/u at the exit, for the yield
calculation of the whole reactor). Plug flow is the best flow regime, not only from the point of
view of simplicity, but above all for excellent performance, giving a high yield of reaction and
a uniform composition of products. It is a difficult task for a process designer to approach this
ideal flow regime by special modifications of continuous apparatuses (rectifying baffles etc.),
and the assumption of plug flow is usually acceptable only for turbulent pipe flows. In the
case that the residence times of particles flowing through an apparatus are different (departure
from plug flow is characterised by the RTD
- Residence Time Distribution) the reactor yield
can be calculated on the basis of the idea, that small groups of particles sticking together are
like tiny closed batch micro-reactors, wandering through the apparatus along different paths
(and with different residence times),
see Fig. 8.14.
The reactor yield is calculated again
according to the "batch procedure": the inlet stream is divided into several small streams
which can be considered for the plug flow regions (in Fig.8.14 it was only 3 streams, with the
residence times t1, t 2, t 3 and mass flowrates
). Then the yield of the continuous
reactor is calculated as the sum of the yields of the batch microreactors having
capacity
,.... at times t1, t2, t3,.... As a measure of the yield we will use the reaction
progress z (yield, amount of any species /in moles/ produced or consumed in reaction is zvi),
and
(8.60)
Terms
are the ratios of mass flowrates of streams with residence time ti over the total
flowrate. If we select the times t1 , t2, ...,t i, ti+1,... equidistantly (i.e., t
i+1 -ti =Dt constant), the
ratio has dimension 1/s and is called the Residence Time Distribution. Using this we can
substitute the sum in Eq.(8.60) by the integral for Dt->0
(8.61)
This means that we can calculate the reaction progress (and therefore the yield) of a
continuous reactor knowing the reaction progress in a batch reactor z(t) and the residence time
distribution E(t). The distribution E(t) depends on the flowfield inside the apparatus and can
be computed or measured; do you remember the example describing the application of
radioisotopes for evaluating residence times in a basin for the waste water treatment process
(Chapter 4, p.13)? The curve plotted by the radiation counter at the outlet of the basin was the
residence time distribution E(t).
This model of fully segregated flow is accurate only for homogeneous reactions of the
first overall order, but can also be used for heterogeneous reactions (solid particle - gas) with
reasonable accuracy, Thın (1998). Reactions of a higher order than one (r>1) taking place
inside the apparatus require a more precise description of the flow structure. The idea of
isolated batch microreactors must be abandoned. How can I explain this qualitative difference
in a simple way?
- Calculation of the reactor yield based on the assumption of segregated flow (macromixing)
gives the same result as a calculation assuming maximum mixedness (micromixing at the
molecular level) for a first order reaction. This conclusion does not hold for reactions of an
order other than one.
- Chemical reactions of the first order are typically monomolecular, i.e., collisions of
reactant A with molecules of the other species have no effect on the reaction rate. Therefore
the penetration of "foreign" molecules into imaginary microreactors from surrounding
streams are of little importance. This is not so for bimolecular reactions, which depend on
the probabilities of collisions between molecules of different species; different
concentrations of reactants in neighbouring streams and molecular mixing between these
streams have a substantial influence on the reaction rate.
The simplest and most frequently used approach is based on the model of an ideally mixed
reactor
, often referred to as a CSTR (Continuous Stirred Tank Reactor). The assumption is the
same as for an ideal batch reactor (i.e., concentrations are independent of location in the
vessel), but the reactor is continuous, there is an inlet stream and an outlet stream, having the
same composition as the mixture inside the reactor. A particle just entering the ideally mixed
reactor has exactly the same chance of leaving in the next instant as any other particle, no
matter how much time it has spent there. Consequently, and unlike the batch or plug flow
reactor, particles leaving the reactor have substantially different residence times, see Fig.8.15
for a comparison of a batch and a CSTR.
Remark: Maybe the figure is slightly misleading, because the particles drawn in Fig.8.14 are changing their
colours continually; in the simple world of inorganic chemistry this is not usually so: a molecule of CO2 either
exists or does not, particles should be either white or black, nothing in between. Only in this case it is possible to
match the distribution of particles inside the CSTR with the distribution in the batch reactor at a particular time t
and only then (at time t) will the rate of chemical reaction be the same in the batch and in the continuous reactor.
The gradually changing state (colour) of particles is typical for bio-substances, composed of continually growing
or decaying macromolecules; this is an unpleasant complication, because it is not possible to find an exact match
between the distributions of reactants and products in a CSTR and a batch reactor. Therefore the data from a
batch experiment or from rate equations like (8.24) should not be used for calculating continuous systems (at
least theoretically). Fortunately, the situation is not as bad as it seems, and even the changes of bio-substances
can be described in a classical way.
As an example of a calculation in a CSTR at steady state we shall suppose that only species A
reacts, and that the reaction is of the r-th order. We shall write equations for the
concentrations of species A in a batch reactor and in a CSTR:
(8.62,63)
where V is the volume of the CSTR and is the volumetric flowrate [m3.s-1]. Equation (8.62)
has been solved (see (8.29)) and Eq. (8.63) is only algebraic and not a differential equation
for a concentration in the CSTR. For the first order reaction (r=1) the solutions are given by
(8.64,65)
Which reactor is better? If we select as a criterion of optimal design the maximum performance
for a given reactor size (internal volume V), it is sufficient to compare (8.64) and (8.65) at a
mean residence time , because at this time the volume of substance processed in the
CSTR is V, the volume of the reactor. Relative decreases of concentrations [A]/[A]0 are:
So, which is less? You have two ways to get an answer: work or think; work involves using a
calculator or a spreadsheet, think involves using your brain, e.g.: exp(kt)=1+kt+(kt)2/ 2+...
(Taylor expansion) > 1+kt . Or simply: for kt->inf and kt=0 both expressions are equal, and for
kt=1 it holds that e>2. Therefore the left side ( exp(-kt) ) is smaller than the right hand side
(1/(1+kt) ) at any time t, and the concentration of species A is lower (and the yield higher) in the
batch reactor. This is an important conclusion: A CSTR, a continuous system with ideal
mixing, has a worse performance than the plug flow continuous system or a batch reactor.
It can
be shown that this conclusion is also valid for chemical reactions of an order higher than one. A
real reactor is always something between these limiting cases, and a very useful model for
describing a nonideal continuous reactor consists of a series of CSTR. A comparison of
- a single
CSTR,
- a series of CSTR, and
- a plug flow reactor
is shown in
Fig.8.16.
Note that there are two
modifications of ideally mixed reactor CSTR, micromixing and macromixing
: the first (and the
worst from the point of view of yield if the reaction order is higher than one) is characterised
by a random distribution of molecules, and the second by random distribution of tiny "batch
microreactors" inside the CSTR. Both variants have practically the same residence time
distribution, but in the first case the conversion is calculated according to (8.65), while the
segregated flow is calculated according to eq. (8.61). The same procedure can be used for a
series of CSTR (segregated and maximum mixedness regimes should be distinguished again),
the only difference being the residence time distribution. I hope that Fig.8.16 clearly
demonstrates that, in the plug flow region, the difference between segregated and maximum
mixedness regimes disappears.
Remark: Residence time distribution E(t) for a single CSTR is an exponential function (see
e.g., Levenspiel (1956)), the time course of concentration of A in a batch reactor for r=1 is also an exponential
function, see Eq. (8.64) and thus integral (8.61) can be integrated analytically
(8.66)
This is exactly the same result, obtained under the assumption of maximum mixedness, Eq.(8.65). This only
supports the previous conclusion that the first order reactions (usually monomolecular reactions) give the same
yield regardless of the segregated flow or maximum mixedness regime. Therefore it does not matter which
method we select for evaluating CSTR series, assuming a first order reaction (micromixing is easier). As the
volume of each CSTR is V/N (N-is number of vessels, V is reactor volume) the material balance of [A] species is
(see 8.63)
(8.67)
and the concentration at the outlet of the last vessel [A]N can be expressed in terms of the concentration in the
preceding vessel [A]N-1 according to Eq. (8.67) and using the definition of the mean residence time .
Repeating this substitution recursively, the following relation between inlet and outlet concentration is obtained
(8.68)
If we increase N to infinity (dividing the actual reactor into an infinite number of infinitesimally small CSTRs,
and preserving volume V) we obtain
(8.69)
and this is the conversion (8.64) of the plug flow reactor!
CSTR and plug flow reactors are basic elements of a kit for the construction of
complex models. These models are suitable for flow descriptions in real reactors, and a series
of CSTRs is such an example. Other examples are parallel series of CSTRs (e.g., a description
of the parallel multiphase flows), models of short cut flows by plug flow units, dead zones or
zones with poor interchange of mass with the mainstream, etc.
The computational procedure
of a reactor described by these models remains, the only difference being in the more involved
calculations of the residence time distribution E(t), which is needed in Eq. (8.61). An
important class of combined models are models of recirculation. The simplest arrangement is
in Fig.8.17.
The recirculation ratio f Î(0,1) is the ratio of flowrate in the recycle loop with
respect to the flowrate through the apparatus.
The interesting thing is: when increasing the recirculation ratio up to 1, the system tends to
behave like a CSTR, like an ideally mixed vessel, regardless of the basic unit used (plug flow
in Fig.8.17). This means that recirculation always worsens the performance (yield) of a
system (there is nothing so bad as a CSTR). This conclusion is rather general: recirculation
has in principle an adverse effect on most continuous processes
(and not only on chemical
reactors - on evaporators, dryers, heat exchangers and sterilisers, too). The residence time
distribution is very widespread, which means that the substance is processed nonuniformly.
Recirculation could be introduced in an university, too: e.g., 90% (f=0.9) of randomly selected students will be
returned after graduation to the first semester. Then you will be sitting in a classroom with tired colleagues of
forty, fifty, or sixty years of age, with beginners and with others who are repeating this course for the tenth time
(these differences of age are characterised by the residence time distribution, E(40) is simply the number of your
40 year old classmates). What a ridiculous picture! Of course, there will also be a positive effect: The number of
students will be increased, and also the university's income. Teaching staff will be instantaneously trained.
There are always good specific reasons for recirculation: increasing f increases the flowrate through apparatuses,
and thus some processes can be intensified - e.g. heat and mass transfer, cleaning of internal surfaces, etc.
Recirculation of flue gases decreases the temperature of combustion, thus reducing the production of NOx.
Recirculation of drying air in dryers saves energy and is required in cases when the dried material does not like
dry air. Etc., etc. Be that as it may, have in mind that the necessity of recirculation indicates that there is
something wrong in the basic system, and what is wrong can be improved (except bad character). Sometimes the
outlet stream is separated, e.g., according to its composition and only the part which requires further processing is
recirculated (this is something quite different, and selective recirculation eliminates most negative effects). This
technique is used, for example, in some bio-reactors, where enzymes (catalysts) are separated by ultrafiltration
and returned to the inlet of the reactor to promote bio-reaction - cultivation of biomass.
@TEC: 3. 3.2003
Change language to
peoples
mailto: Zitny