Example 7.3: Gas lighter.
The previous analysis was rather difficult and tedious,
so we shall try something easier and more fun. Look at the following sketch of an ordinary
gas-lighter.
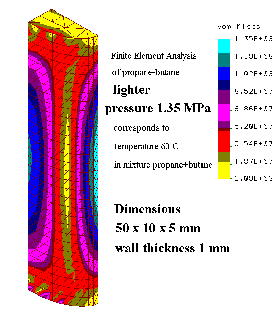
The question is: What substance or
what mixture is to be used for filling the lighter? The first requirement is that the substance
should be flammable, and hydrocarbons are a good choice from this point of view. The
substance should also be a liquid at ordinary temperatures (say from -20 to 600C), therefore
the critical temperature must be higher than 600C. Why a liquid and not a compressed gas?
If
equilibrium between the liquid and vapours is attained, the pressure of the vapours depends on
temperature only and not on the amount of filling. Therefore the pressure of the vapours will
be the same no matter if the lighter is full or almost empty. The performance of the lighter will
not decrease during its use.
We have not yet presented critical temperatures in a table, but the Tc values can be evaluated
from the parameters a,b of the van der Waals equation, using (5.8): Tc =8a/(27Rb).
Substituting parameters a,b from Tab.5.1 we ascertain that methane CH4 has a critical
temperature Tc = -83.30C and therefore cannot be liquefied at our temperature range. Ethane
C2 H6 also has too low a critical temperature Tc =320C and only propane C
3 H8 (Tc =97 0C) or
butane C4 H10 (Tc =1520C) remain as possible candidates. The performance of the lighter can
be assessed according to the phase diagram p(T) of ethane, propane and butane (I assume, that
you are able to construct the graphs using the parameters of the Antoine equation in Tab.7.1),
Fig.7.7.
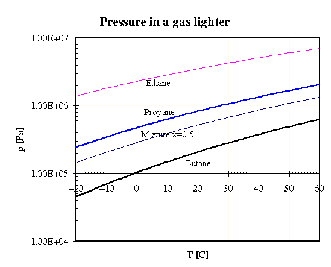
Filling with butane is apparently applicable
only at temperatures above 00C, otherwise the pressure of the vapours would be less than
atmospheric pressure, while propane exhibits pressure too large at 60 0C (2 MPa) so that the
lighter would have to be robust.
Therefore a propane+butane mixture seems to be the best compromise (see the
curve in the phase diagram corresponding to the constant composition of the liquid phase
xButane=0.5). The composition of vapours yButane differs from xButane, and can be estimated (the
problem is much simpler than that, solved in example 7.2, because we need not consider the
constraint of constant pressure). Assuming that the propane + butane mixture is nearly ideal,
Raoult's law, pA = xApA" , can be a good approximation
,
see Fig.7.8.
It is obvious that the "heavier" component (butane) evaporates less than the "light" component
(propane). Therefore the concentration of butane will increase during the life of our lighter
and its behaviour will change. To ascertain how, a time simulation must be performed. The
lighter is a typical batch system, where all important quantities, composition of liquid/gas
phases and the total pressure, depend on time. The time simulation of such a process is based
on mass balances, which will have the form of differential equations.
I have declared that the most important engineering art is the ability to simplify. I
add one more: the ability to translate words and sentences from a "human" language into the
language of mathematical symbols, e.g., equations. This is much more difficult than
translation between English and German, but this is what you will be paid for. And this
example is a suitable occasion to begin learning and practising the art:
Human language: "The decrease in the amount of butane in the lighter within one second
equals the flowrate of butane leaving the lighter in the vapour mixture. This flowrate is
directly proportional to the flowrate of mixture and to the fraction of butane in the
mixture".
Mathematical language:
,
where n Butane (t) is the amount of butane (in moles) remaining in the lighter at time t (therefore
-dn Butane/dt is the amount of butane leaving the lighter within one second - molar flowrate),
and is the total molar flowrate of the gaseous mixture (moles of butane + propane that burn
per second). The time derivative dnButane /dt characterises the time rate of increase and not
decrease of nButane, and this is why the negative sign appears on the right hand side of the
equation.
The second equation, describing the material balance of propane is almost the same,
,
where the obvious identity between molar fractions in vapours y Propane =1-y Butane
has been used.
The simplest way to integrate the system of differential equations is to replace the
derivatives by ratios of small differences, e.g., dn Butane /dt by Dn Butane /Dt. The number of butane
molecules remaining at a time t+D is n Butane (t+Dt)=n Butane (t)-Dt. .y Butane
(t). This procedure
can be realised in Excel (constant temperature T=250C and initial molar fraction x=0.5 is
prescribed in the following sheet; only rows 1,2,3,4,5 are presented, others are copies of the
fifth row /each row describes one time step of simulation/):
Column C, containing the amount of mixture (in moles) that has been consumed at time t, is
used as the independent variable in Fig.7.9 (columns D,E,F are dependent variables, molar
fractions of butane xA,yA and total pressure p). You can see that at the end of our lighter's life
all the propane is exhausted, the vapour pressure is low, and the lighter's performance
deteriorates.
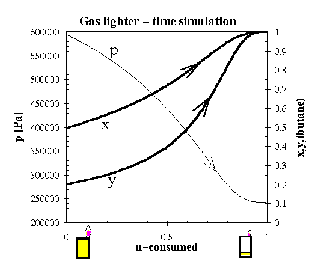
This procedure ends the thermodynamic analysis and the mechanical design
begins. The most important parameter is the maximum pressure that can be expected during
operation (in our case it was 1.35 MPa, corresponding to a 50% mixture of propane and
butane at 60 0C). Dimensions, material and the shape of the lighter are designed respecting
ergonomic and aesthetic criteria. Even then the estimated thickness of the walls is tested
using, e.g., a finite element method (substituting a real lighter by a mathematical model), and
loading the inner surface by the design pressure, see Fig.7.6. As a result we obtain the
distribution of stresses acting in the shell of the lighter corpus (max. stresses are 135 MPa /see
top of chart in Fig.7.6, denoted as von Mises/), and according to this we should modify the
design, e.g., the thickness of the wall (the peak stress 135 MPa is too high for plastics).
I promised the easy example, but it turned out to be pretty complicated.
Nevertheless, if you understood at least the principles, you have learned a lot of skills that can
be applied in other branches of mechanical engineering. By the way, the phenomena
mentioned in Chapter 6.3 (transient heating, phase changes, boiling of mixtures) and the
periodical distillation described in this chapter can be simulated in the same way as the
processes in our gas lighter.
@TEC: 3. 3.2003
Change language to
peoples
mailto: Zitny